Compliance Made Simple
(Overcladding High-Risk Projects)
Introduction
The Building Safety Act 2022 (BSA) and secondary legislation in 2023 represent a pivotal moment for the construction industry placing an absolute focus on building safety, especially in respect of fire spread and structural stability as a result of the Grenfell tragedy.
The BSA introduces new roles and responsibilities and places an emphasis on Clients delivering high-risk projects to ensure the Building Regulations (which remain unchanged), are met.
It recognises that the client decisions taken at the outset of a project are the most influential for the outcome of the project. The Act now requires clients to set out how they intend to deliver the project. To give clear roles and responsibilities to the dutyholders which will give clear recourse in the event of future problems. The Client is solely responsible for how they assess the competency of those they elect to appoint.
We fully support this aim because, in our experience, this is precisely where ambiguities arose that led to the overcladding industry’s failure on an unprecedented scale.
Clients responsibilities
(1) the client (the building owner or representative) is the accountable person responsible for making key decisions at the outset including…
(2) identifying a clear project delivery process (Form of Contract) to deliver the golden thread with clear roles and responsibilities to remove ambiguities and instil extra vigilance and…
(3) assess the competency, skills, knowledge, experience and behaviours (SKEB) of those they propose to appoint by taking reference from their past performance, including most notably failures, that must now be disclosed in advance and then…
(4) monitor the delivery process through all BSA gateways through to comprehensive handover on completion of all documentation and warranties.
If this legislation is understood and implemented correctly, key decisions made by the Client at the outset which determine a project’s outcome will bring about a polar change within the industry.
A clear project delivery process
There are 3 project delivery processes the clients ‘accountable person’ may adopt:
1. TRADITIONAL
Under this structure, the accountable person appoints the ‘employer’s design team’ comprising consultants to carry out the feasibility and design stages including architects, structural and M&E engineers as well as other specialist professionals to complete the ‘design’ and specify or prescribe the products to be used. The consultants will each be liable to the employer for their respective design failures, but only where the failure arose out of that professional’s failure to exercise reasonable skill and care. If the design specifies novel or specialist products or systems, the supplier may take some responsibility for their system design failures. In this traditional process, the contractor does not have design obligations yet must construct in accordance with the design provided by the employer’s design team. The contractor is then liable for construction defects. Legal difficulties frequently arise where failures are a result of a combination of design, material, system selection and workmanship deficiencies. The process is thus fundamentally flawed.
2. DESIGN AND BUILD
Under this structure, the accountable person appoints the Specialist Contractor to be singularly responsible for feasibility, design, material and system selection and construction with an expressed warranty that the works will be fit for purpose for an agreed period. Responsibilities often include the existing structure’s ability, repair and long-term suitability to withstand the imposed loads. In this best-in-class process, the Client has clear recourse to the contractor for any failure irrespective of being either design, material selection or workmanship. This responsibility extends to where a contractor designs a building to use a material or system in a novel or unusual way – the contractor remains wholly liable. The consequence is that a design and build contractor will be liable where a traditional architect or engineer would not be because the contractor will not have a “state of the art” defence – there are no ambiguities.
3. HYBRID
This structure is as it sounds, an ambiguous combination of Traditional and Design Build processes where the accountable person appoints the ‘employers design team’, consultants to carry out the feasibility and design stages as in the Traditional process and then the project is tendered to contractors who will be required to quote on the consultants’ design that will be novated to them if successful. The Design and Build contractor will generally then be liable for the entirety of the design and the consultants will be absolved of liability for their designs. Under this scenario, difficult issues arise where the root cause of the problem was a design decision or material selection taken prior to tender. The contractor may then be able to say that the design defect was part of the scope of the design they were obliged to construct. Whilst this manner of contracting might on the surface look like the design and build mechanism, it seriously dilutes responsibilities and presents major possibilities for a project to go wrong, for example:
3.1 The employer’s design team are informed by aesthetic considerations or system suppliers. The ACM suppliers secured specifications from client design teams and then expressly excluded design and product responsibility from the contractors they supplied.
3.2 with no contractor involvement, designs are not informed by buildability, product warranties, and/or levels of disruption that their design will cause with the net effect that either:
• contractors may submit tenders assuming all is well with the design, or
• decline to participate in a flawed process, or
• seek to offer alternative designs or submit high prices to reflect the cost of delivering a flawed design.
None of these options comply with the BSA nor have good short or long-term outcomes for the Client. In these scenarios, the employer obviously seeks redress for failure from the Contractor and the original design team’s responsibility falls away as exemplified by the debacle at Chalcots, the Contractor will naturally defend themselves via ‘I built exactly what you told me to’. Whether that affords the Contractor a robust defence will depend upon the precise nature of the defect and the terms and conditions of the contract, however, should this argument transpire to be weak the contractor closes up shop very quickly leaving the employer chasing an adversarial PI insurance organisation. Irrespective of the eventual outcome, the employer faces years of litigation with uncertain outcomes, all whilst owning a failure, and ultimately has to go through the entire process once more. The hybrid mechanism is known in the industry as ‘design & dump’ – but in the terminology of the Building Safety Act, it might be termed ‘the broken thread’.
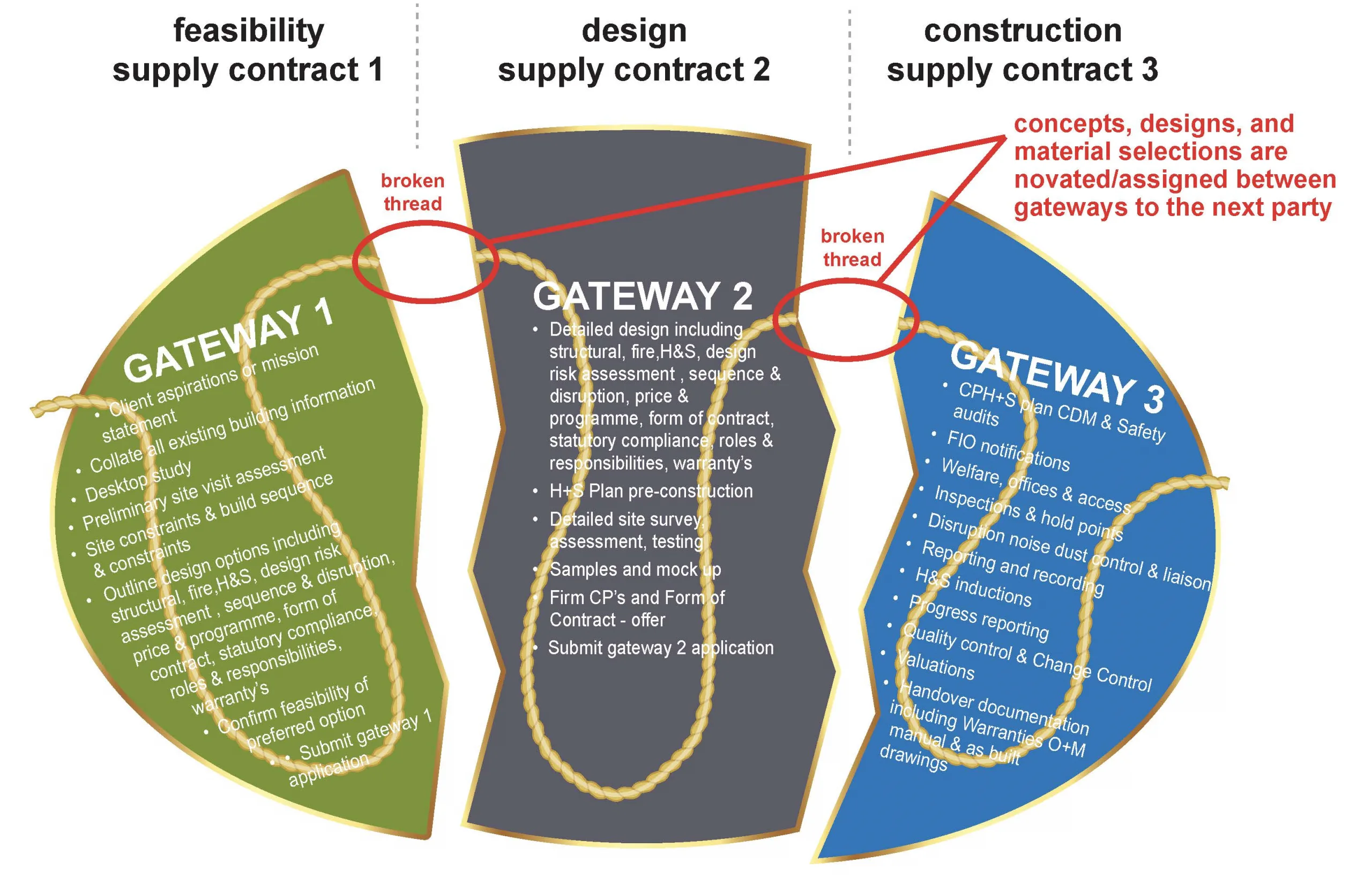
There is only one Form of Contract in existence suitable for high-risk projects that makes one party singularly responsible for the end product being fit for purpose and makes that party extra vigilant to use the very best materials and methods to ensure performance and standards are met, that is a pure Design Build Form of Contract. It precisely defines clear roles and responsibilities and ensures the Golden Thread of information is seamlessly fulfilled. This procurement route demands that the Principal Designer and Principal Contractor appointed by the Client at the outset are one-and-the-same.
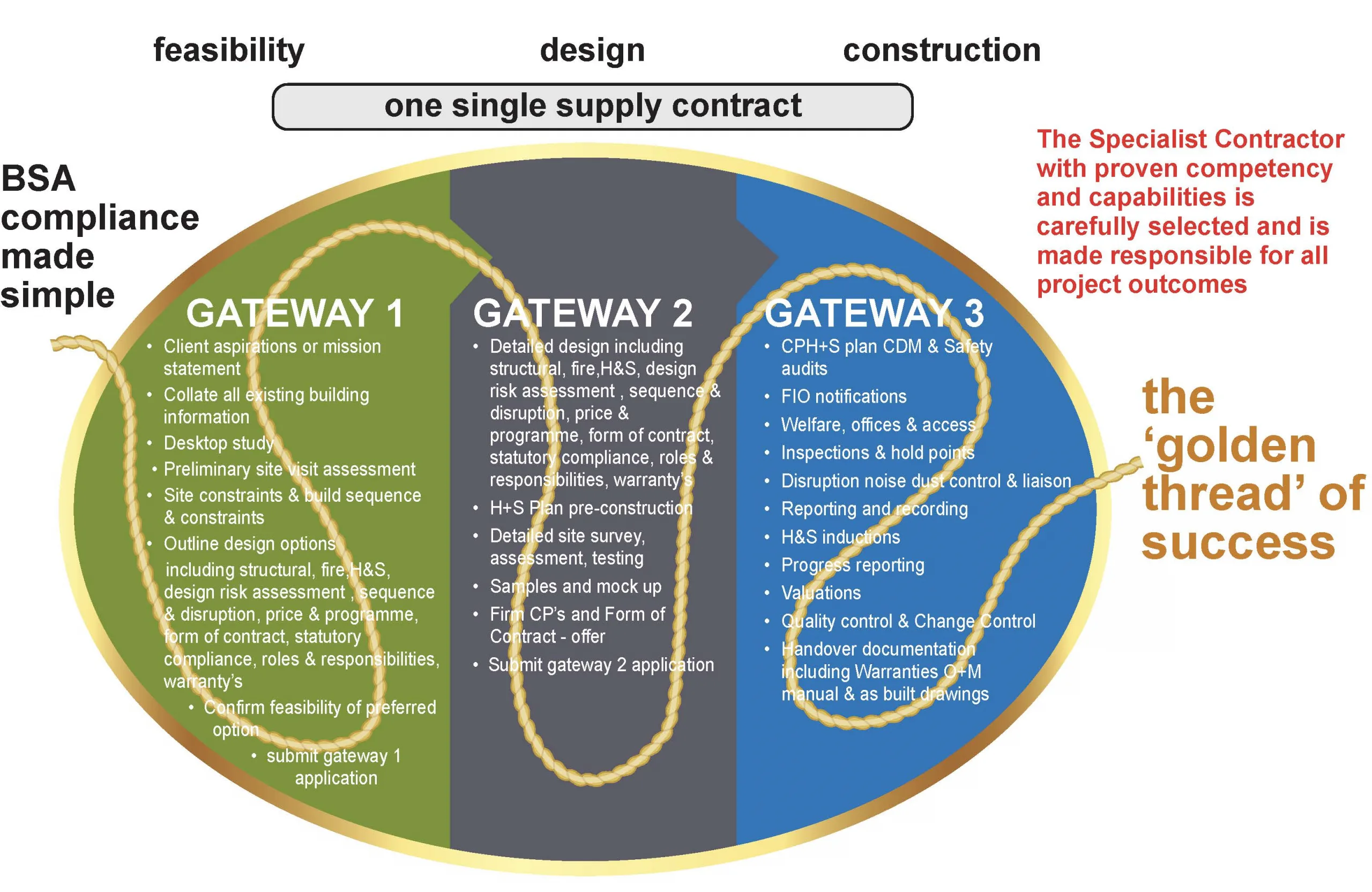
Assessing competency
The Building Regulations etc. (Amendment) (England) Regulations 2023 (BRAE Regulations) make clear it is the Client’s responsibility, having carefully selected the delivery process, to ensure that the proposed appointees possess the necessary Skills, Knowledge, Experience and Behaviours (SKEB) to fulfil their duties.
Optimising procurement
Procuring Design Build services is extremely simple and efficient.
The Client invites tenders via simple outline enquiries posing a very simple question to tenderers, i.e. “here is my building, and outline Employer’s Requirements or aspirations, you are invited to submit detailed offers (Contractor’s Proposals) together with all supporting evidence to demonstrate your competency and ability to deliver the project to meet or surpass the standards with minimal risk or disruption and maximum certainty of outcome complete with sample warranties”.
The Client then undertakes robust due diligence interrogating tenders based on a careful assessment of all past performance and the very detailed Contractors’ Proposals (CP’s) for the works including typical tender deliverables as follows (NB: it is vital that tender deliverables are weighted heavily to reflect the required SKEB:
TENDER DELIVERABLE | ENCLOSED | SCORING % |
---|---|---|
Price Analysis Bill including prelims breakdown including fixed price for the pre-construction phase and budget price for the construction phase with provisional sums where required and extra over prices for options where it is possible to surpass minimum standards. | 25 | |
Fixed programme for preconstruction works including obtaining statutory approvals and provisional programme for the construction phase, showing anticipated lead-in, testing, materials ordering, site set up and period on-site for carrying out the works and subsequent clearing site. | 5 | |
Confirmation of preferred Form of Contract including terms and conditions, period and specimen warranty & bond. | 5 | |
Last 5 years audited accounts, Company details including health & safety policy, & details of all insurances including PI. | 10 | |
Full details & references of any/all similar projects carried out previously including failures. | 5 | |
Declaration of non-collusion | Pass/Fail | |
Contractors proposals document comprising:
1. Full narrative descriptive details of proposed external cladding and overroofing together with the following indicative drawings, sections & details. 1.1 Typical vertical & horizontal sections of the external walling detailing the profiles of members, the integration of windows, driven rainwater management, condensation, drainage, and mullion-to-transom connection method with areas for any site-applied sealants shown, and including sectional details overlaying the proposed system onto existing wall sections. 1.2 Details of proposed connections to the structure for cladding showing bracketry and all secondary structural supports. 1.3 Details of flashings, fire & smoke stops. 2. Project-specific method statements & risk assessments including methodology to cover each of the following: 2.1 Identified hazards 2.2 Demolitions & takedowns 2.3 Installation of new works 2.4 Proposals for minimisation of disruption, safety of building users, maintaining weather protection, security, and all temporary protection works required. 2.5 Protection of internal fixtures and fittings 2.6 Site establishment plan drawing showing location, and maintenance of fire escape routes, protection of entrances, walkways & roadways and methodology for deliveries, offloading, site distribution, and on-site storage. |
35 | |
Full details of proposed products, suppliers & subcontractors. | 10 | |
Specimen warranties & guarantees stating the period and life expectancies of all major products and materials. | 5 |
By following this simple process carefully, the Client is assured of absolute regulatory compliance, certainty of outcomes and an end product fit-for-purpose.